Polyethylene Injection Molding
Polyethylene is widely recognized as one of the best thermoplastic materials on the market. Its intrinsic resistance to impacts and extreme flexibility makes it the perfect choice to manufacture durable components for several industries.
On this page, we will delve into the operational advantages of polyethylene injection molding. You will also find out more about how Idea Stampi can effectively respond to the market’s demands through small, medium and large scale productions for a variety of sectors and how we perform the process delivering impeccable tailor-made solutions for your business.
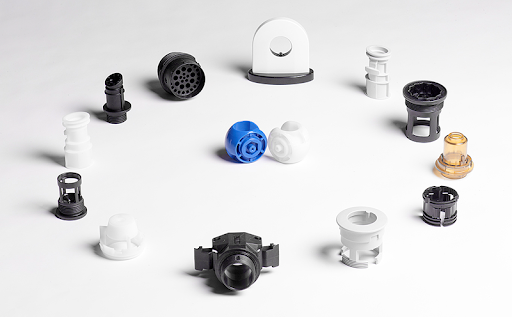
How Does Polyethylene Injection Molding Work?
Polyethylene injection molding is a highly performing and flexible procedure which consists of transforming the material into durable components.
These are the phases of the process.
- Polyethylene is fed into an injection molding machine, where it melts. Temperature may vary, but the final result is a flowable plastic material with optimal viscosity.
- Once molten, the technopolymer is injected into a mold cavity to take the shape of the final product. In this phase, polyethylene must fill every part of the mold. The speed and the pressure of the injection can affect the quality and features of the final output.
- Then, polyethylene solidifies within the mold. This procedure is handled with specific cooling systems that harden the material into a solid state.
- Ultimately, the finished product is extracted from the mold.
The Operational Benefits of Polyethylene Injection Molding
Polyethylene is a thermoplastic polymer which is widely used in manufacturing applications thanks to its physical and chemical properties. Its inner structure guarantees the consistency of the injection molding procedure for large scale production of complex designs for specific applications.
Among the most interesting advantages of polyethylene, there are:
- Variable density: the spectrum of polyethylene encompasses low-density polymers (LDPE) and high-density materials (HDPE). These two different varieties of the same thermoplastic allow to work with different rigidity and heat resistance levels, depending on the components you need to manufacture.
- Lightweight: polyethylene is easy to work with due to its inherent flexibility, implying lower transportation costs.
- Resistance: this material is the ideal choice for those sectors that require extremely solid polymers which can withstand impact, stresses, wear and tear as well as corrosion caused by organic solvents and aggressive chemical agents.
- Waterproof: polyethylene is water-resistant. It also provides excellent insulation in electrical applications.
Learn more about polymer injection molding at Idea Stampi
Read here
How To Apply Polyethylene Injection Molding To Several Industries
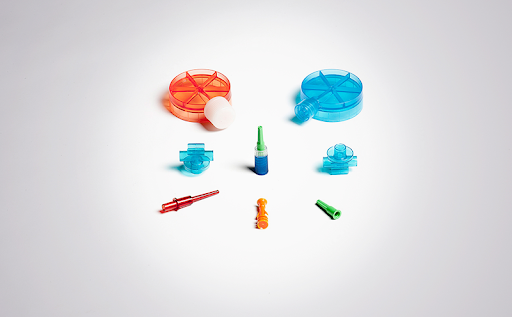
Polyethylene is used for a vast range of solutions in different sectors due to its adaptability. These are some of the most common applications.
Automotive Industry
Polyethylene injection molding is unparalleled when it comes to the automotive. In this sector, durability, functionality and lightweight materials are instrumental to realize scalable components that can guarantee excellent, long-term performance. Fuel tanks, ducts, interior trims can be manufactured using HDPE as it features a perfect strength-to-density ratio which minimizes vehicle emissions.
Electronics Industry
PE is largely employed in the electronics field thanks to its insulating properties. It can be used in the creation of housings for electronic devices, protecting them against mechanical impacts and chemical corrosion. Furthermore, its dimensional stability is valuable in applications where every part must fit specifications that can affect their functioning.
Medical Industry
Polyethylene injection molding can also be used for manufacturing containers for medical supplies, prosthetics, and lab ware. Being a sterile material, it is a safe polymer to employ in sensitive medical environments where cross-contamination must be avoided at all costs, especially during medications.
Tools not only have to be properly sanitized, but they also need to be biocompatible and easy to be disposed of. As PE is 100% recyclable as well as corrosion resistant, it is the perfect material for this kind of sector.
Why Should You Choose Polyethylene For Your injection Molding Procedure?
As we have mentioned above, polyethylene is ideal when it comes to injection molding as it is easy to work with due to its versatility.
However, there are four parameters that can be adjusted during the process which directly influence fundamental characteristics of the material, such as:
- viscosity, as to say the texture of the polymer, which is impacted by the melt temperature. This factor can be manipulated to enhance flow properties to fill cavities more consistently.
- molecular weight or the mass of the molecule of a specific substance.
- transparency and, consequently, the opacity of the end product. This feature is determined by mold temperature.
- injection speed and pressure are crucial elements that need to be considered as they can affect the final quality of the product. Controlling those two factors can prevent incomplete filling and imperfections that could be detrimental to the entire process.
Discover more about how polyethylene injection molding is performed at Idea Stampi
Contact us for more information