Plastic Injection Molding Of Medical Parts
Are you in need of a specific medical part? Idea Stampi can manage the whole production injection molding process, from the mold prototype to the finished product.
Everything related to the medical sector must comply with specific rules dictated by the FDA. This means that any tool, or part of it, used in the medical sector must be approved. Idea Stampi is able to carry out injection molding of medical parts, from prototyping to the finished product, in absolute compliance with the law.

Plastic injection molding for the medical sector: the mold prototype
Our area of expertise lies in constructing suitable molds for plastic injection molding. This process involves injecting the mold prototype into a mold cavity, where it cools and solidifies into the desired shape. In the medical sector, injection molding is used to manufacture a wide range of products, from syringes and IV tubing to surgical instruments and medical device components.
To create a mold prototype for medical plastic injection molding, several factors must be taken into consideration. These include the material to be used, the design of the part to be molded, and the production volume required. The first step in creating a mold prototype is to design the mold itself. This typically involves using computer-aided design (CAD) software to create a three-dimensional model of the mold. The mold design must take into account factors such as part geometry, parting line placement, gate location, and cooling channel placement.
Advantages of using plastic injection molding for medical parts
Plastic injection molding offers numerous advantages for manufacturing medical components, making it a preferred method in the healthcare sector.
Some of the most significant benefits include:
- Cost efficiency - economies of scale achievable with injection molding significantly reduce the cost per unit, especially important in high-volume production of medical parts.
- High precision and consistency - the injection molding process allows for high-precision manufacturing of complex shapes, crucial for medical devices that demand stringent tolerances.
- Material versatility - the ability to use various biocompatible plastics that can withstand sterilization processes and resist chemicals and wear.
- Speed of production - once the mold is designed and created, parts can be produced at a rapid rate, which is vital for meeting the increasing demands of the medical industry.
- Reduced waste - injection molding is a sustainable manufacturing option, as it generally produces less waste compared to traditional manufacturing methods, aligning with the industry's move towards sustainability.
By leveraging these advantages, Idea Stampi delivers superior quality and highly reliable plastic injection molded medical parts that healthcare providers can trust.
Key medical parts made through plastic injection molding
Plastic injection molding is pivotal in producing an extensive range of medical parts that are integral to modern healthcare. At Idea Stampi, we specialize in crafting high-precision components tailored to meet stringent medical standards.
Here’s a glance at some of the key products we can manufacture:
- Medical housings - durable and sterilizable enclosures for devices such as MRI machines and ultrasound equipment.
- Surgical instruments - lightweight, precision tools including forceps and scalpel handles used in various surgical procedures.
- Drug delivery systems - components for single-use syringes, insulin pens, and sophisticated auto-injectors ensuring precise dosage and patient safety.
- Implantable components - biocompatible materials used in orthopedic implants like knee joints and dental implants for long-term body implantation.
- Diagnostic equipment - critical parts for devices that require high accuracy, such as components for blood pressure monitors and components for glucose meters that ensure reliable readings.
Our manufacturing process ensures that each product meets the rigorous quality and reliability demands of the medical industry.
Testing and construction of the mold
Once the medical mold prototype is completed, the test phase begins. The mold is put in place and produced some test pieces to understand if they meet the defined needs of the customer. Eventually, adjustments are made and we return to the design phase. Once the final result is obtained, the customer can choose whether to buy the mold and include it in their production line, or whether to entrust the entire production process to us. In fact, we are able to supply both semifinished medical parts and finished products ready for use in the construction of purchased instruments or directly in medical facilities.
Managing the plastic injection molding process of medical parts
Managing medical injection molding requires strict adherence to quality control measures and industry regulations. Here are some key steps to consider:
- Choose the right materials: select materials that meet the requirements for the specific medical application, including biocompatibility, durability, and sterility.
- Optimize the mold design: the mold design should be optimized for the specific medical part to ensure consistent production and quality.
- Implement process validation: the injection molding process should be validated to ensure that the parts produced meet the required specifications and quality standards. This involves testing and analyzing samples from the production process to ensure that they meet the required specifications.
- Establish quality control measures: implement quality control measures to ensure that each part meets the required standards. This includes monitoring the process, performing quality checks, and documenting the results.
Overall, managing the plastic injection molding process for medical parts requires a focus on quality control and compliance with industry regulations to ensure that the final product is safe and effective for its intended use.
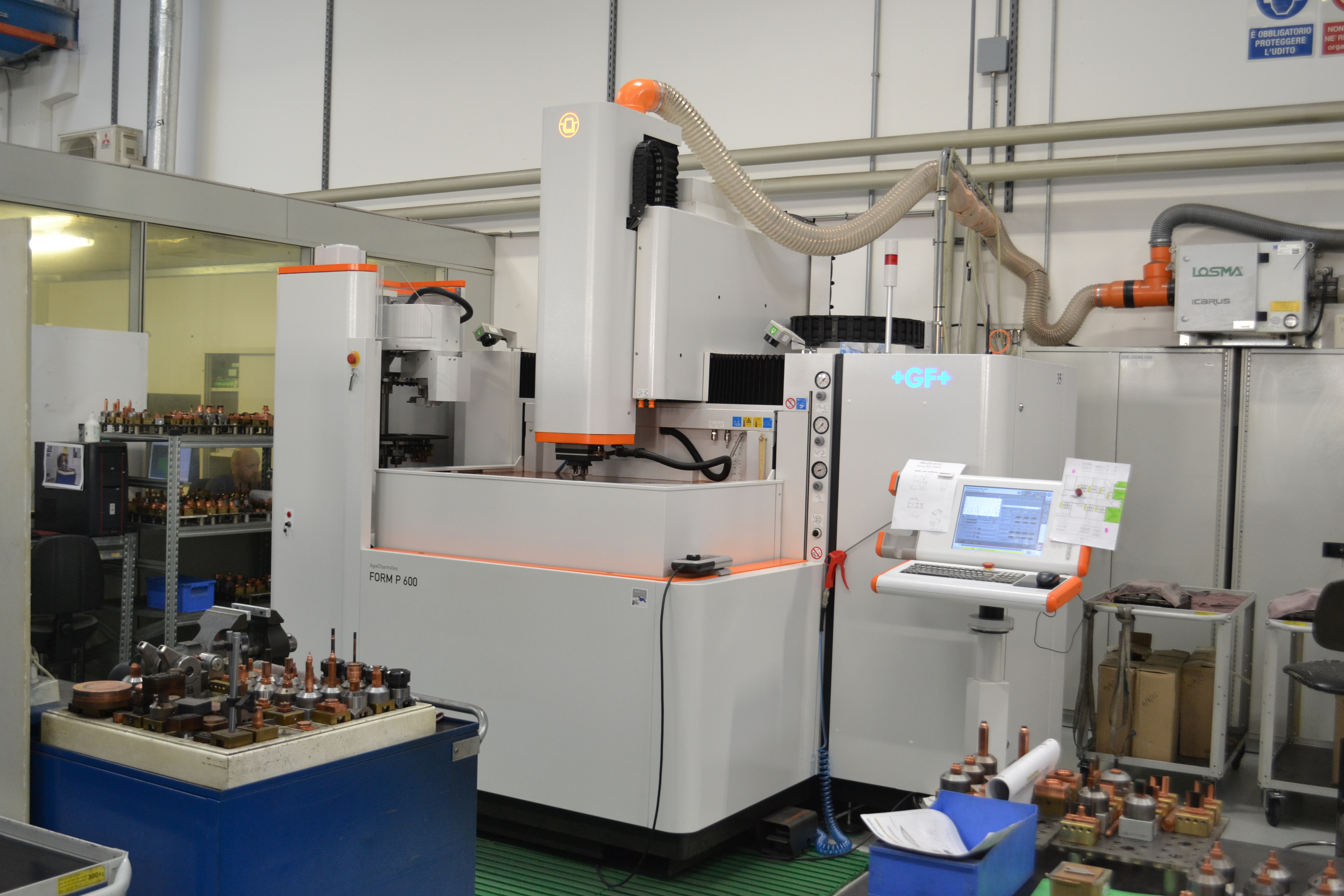
What are the most suitable materials for plastic injection molding of medical parts?
Idea Stampi recognizes the significance of materials in medical plastic molding, as the end products must adhere to FDA regulations. To ensure compliance, we utilize medical-grade plastics that possess high molecular weight and exhibit chemical and heat-resistant properties. For injection molding in the medical industry, the most appropriate materials are:
- polycarbonate PC
- polyether ether ketone PEEK
- Ultem
Polycarbonate PC is widely used for medical tubing due to its remarkable tensile, flexural, and shear strength, as well as its resistance to heat and low moisture absorption. PEEK, a plastic resin that is highly resistant to chemicals, fatigue, and cracking, is suitable for food contact, and medical devices made from PEEK can be sterilized by an autoclave. Ultem, on the other hand, is an ideal plastic material to use in medical devices because of its resistance to environmental stress and high temperatures, as well as its exceptional dimensional stability.
The strict requirements in the medical sector
As mentioned, the medical sector applies strict controls at all levels, including medical and orthodontic instruments used in public and private facilities. The Food and Drug Administration is the controlling body, and its laws must be subject to the companies operating in producing injection molding of medical parts. Thanks to its many years of experience, Idea Stampi guarantees an absolute level of safety, in compliance with US and European laws in manufacturing molds and finished products for the medical sector.
Contact us for a quote