Injection mold design
Since 1986, Idea Stampi deals with plastic injection mold design and manufactures molds for mass production, guaranteeing precision, customization, speed, and after-sales assistance.
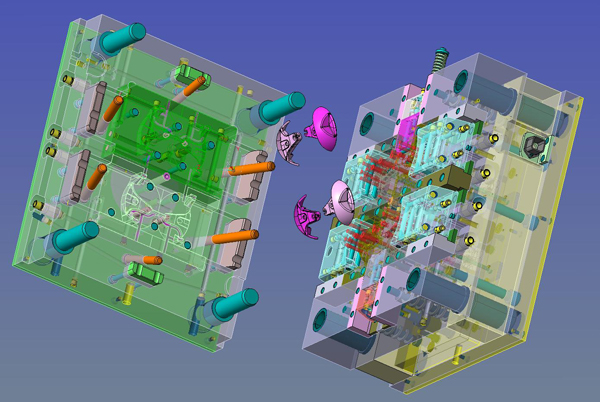
Injection mold design and engineering
Injection mold design involves accuracy, advanced technology and the utmost carefulness in dealing with the entire process.
But how should the mold be used?
What are the products that can be manufactured through injection molding?
How does the item manufactured fit to other components in the assembly procedure?
These are just a few questions that engineers need to take into consideration when starting to design an injection mold.
As a matter of fact, processing issues play a major role in injection mold design and engineering. For instance, analyzing how the molten materials enter, fill, and cool within the mold allow engineers to design products that are:
- easy to manufacture
- easy to assembly and change within the machine
- strong and wear resistant
- cost-saving
Essential parameters in plastic mold design
From the initial draft up to the 3D design and modeling, there are a series of parameters to keep in mind in injection mold design.
Choose the right material
There are many materials that can be suitable for injection molding. Sometimes this can be confusing, but there are core characteristics that make some materials better than others for injection molding design.
Plastics are perfect for this type of work as they consist of polymer chains. The inner composition of these chains could be subjected to significant modifications that can alter the plastics’ properties and performance.
Two are the main categories in which plastics can be classified:
- thermosets: in this case, an irreversible chemical reaction generates bonds among the polymer chains. This enhances the material resistance to high temperatures. Epoxy, silicone, polyurethane, and phenolic are part of this group.
- thermoplastics: when heated, this kind of plastic becomes malleable and easy to inject. Unlike thermosets, they can be reprocessed and they can be semi-crystalline and amorphous.
Another element which directly depends on the material choice is that of critical tolerances. They can be influenced by process control and tool design as well.
Pay attention to sink marks
In the injection molding design process, core and thicker components need more time to cool down.
As a result of this inconsistent cooling, the dense section pulls inward, leading to a depression on the part's external surface or, in severe cases, distorting the entire piece, increasing the internal stress of the part itself.
In order to prevent this from happening, the maximum wall thickness at the base of a support rib or boss should usually be less than 60% than the perpendicular face wall.
Choose carefully the location of the gate
A crucial element that could affect the whole injection mold design process in terms of aesthetics, tolerance, warpage, surface finish, wall thickness, and so on is the location of the gate.
The gate is the entry point from where the materials are injected into the mold’s cavity. For this reason, it is instrumental to perfectly assess its design, type and location in order to prevent potential distortions.
Deal with shutoffs and draft angle orientation
The shut-off angle is the minimum angle which can be found between core and cavity. Together with the draft angle, these are key factors that can directly influence and alter parting lines, the tool design, the assembly and the cost of the entire project.
Texture and draft are proportional
Texture significantly contributes to the whole component’s aesthetics. It can be used to cover imperfections on the surface and it’s proportional to draft.
In fact, the rougher the texture is, the greater amount of draft you will need. A steeper draft angle ensures that the texture doesn't stick or scrape against the molding surfaces during ejection.
Only after considering all these variables, designers and engineers can actually start the design phase of the injection molds and, once it is concluded, it’s time to schedule critical start-up phases and check if the designed mold actually works.
Are you interested in injection mold design for your project?
Play it safe: contact us for a free quote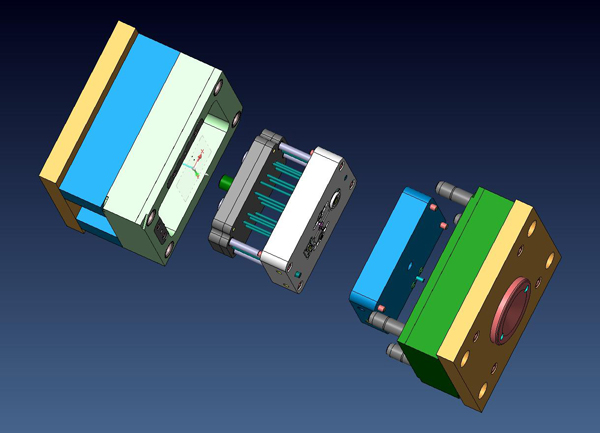
How we approach plastic injection mold design
The core of our business lies in our name: “Idea Stampi” means “Molds Idea”. In fact, we carry out the whole construction process of a mold in-house, from the design and the testing of the manufactured mold up to its delivery to the final customer.
Nowadays, injection molding is one of the most used methods to manufacture goods and components for a multitude of industrial applications and production volumes, each requiring properly designed molds such as:
- injection molds for small or niche series
- injection molds for medium production series with a consumption of 50-100.000 parts per annum
- multiple-impression injection molds for high-volume productions.
When you contact us, the first thing we do is talk to you in order to understand your deepest needs as well as the field you work in. In this way, we can build a product that meets all your requirements.
We start from a co-design phase in which we can discuss directly with you the general design your mold should have. Furthermore, we will decide the aesthetics of the component and the most suitable material based on its employment.
Then, our designers and engineers will start the actual injection mold design stage relying on state-of-the-art technologies such as CAD/CAM/CAE softwares and integrated stamping simulation with VISI Flow systems. That also allows them to carry out some important analyses to define the best position of the gate and optimize thicknesses and conditioning.
Finally, the designed mold is manufactured and tested through presses from 25T to 350T.
Plastic molding engineering also helps fix the molds
It happens that intense use wears out the injection mold design, but Idea Stampi has the right solution: a maintenance service that ranges from standard cleaning up to more complicated interventions such as the reconstruction of worn parts.
Taking into consideration all the above mentioned variables, our molding engineering and technical department can fix your molds within 24/48 hours (if you cannot manage long downtime).
What’s more, this service also applies to molds that have not been designed or manufactured by Idea Stampi.
Are you looking for fully customized injection mold designs?
Play it safe: contact us for a free quote