Automotive Injection Molding
Relying on plastic molding means improving safety, increasing fuel efficiency and ultimately researching for new materials that decrease environmental impact. So, it is not by mere chance that plastic components made from materials like polystyrene, polypropylene or polycarbonate have taken on an important role in the automotive industry.
What does automotive injection molding refer to?
When we talk about automotive injection molding, we refer to the production process that shapes plastic car components using specific molds. The polymers are injected into the cavity by maintaining high-pressure conditions. Once the mold is filled, the plastic material inside cools down, delivering the final product at the end of the process.
Thanks to new state-of-the-art technologies, automotive injection molding is widespread as it allows manufacturing numerous parts in a limited period of time due to the use of automated machines which have greatly accelerated the production flow.
Why should you choose this method?
- It can be applied to the manufacturing of many different car parts.
- The final surface finish is smooth, with no imperfections
- Automotive injection molding can increase the whole mass-production rate without compromising the quality of every single piece.
- It is highly accurate and it significantly reduces energy consumption and waste.
All the automotive parts we can produce through plastic molding
We use injection molding to manufacture a wide range of automotive components such as:
- Fans
- Pump units
- Brackets
- Interior trims
- Door handle components
- Sunroof components and assemblies
- Shifter Knobs and assemblies
- Radiator parts and oil pans
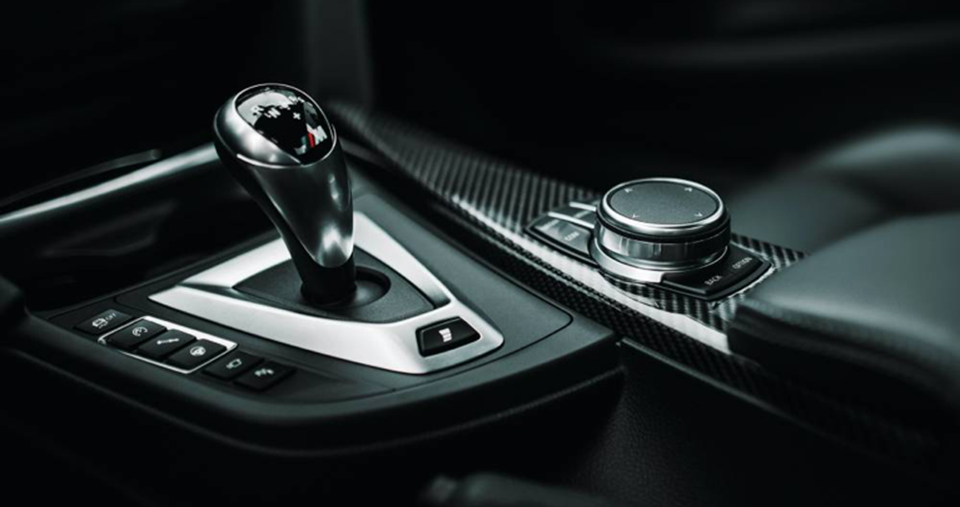
Different parts of the car require indeed different types of plastics according to their chemical and physical properties. The most used in the automotive plastic molding field are:
- Polyurethane PU and other polyolefins which can be easily modified with a broad range of chemical modifiers
- Polyvinyl Chloride PVC
- Polypropylene PP which can be reinforced with fiberglass
- ABS, PET and Nylon, mostly used for under-the-hood elements do to their robustness
Depending on your specific needs and wants, we can advise you on what are the most suitable materials for your automotive components.
Contact us free for charge
Interior and exterior automotive injection molding
Plastic molding is undoubtedly useful for producing a wide range of components for cars and other vehicles, whether they are placed on the inside or outside.
Here are some examples.
Exterior plastic components
Fenders, grilles, door panels, bumpers, light housing, splash guards are just some of the plastic components that can be obtained through automotive injection molding. The main reason lies in the fact that the plastics used in the production process are flexible and resistant so as to minimize debris and splashing.
Interior plastic components
Injection molding finds application in the automotive field also for producing interior decorative elements, surfaces, door handles, air vents, dashboard faceplates and various kinds of instrumentation which are resistant and easy to clean and sanitize.
Under-the-hood components
Nowadays, the radiator, the brakes, the cylinder head covers, the oil pans and other under-the-hood components are made from plastic. Basically it is because it is lower-weight than metal and more easily workable.
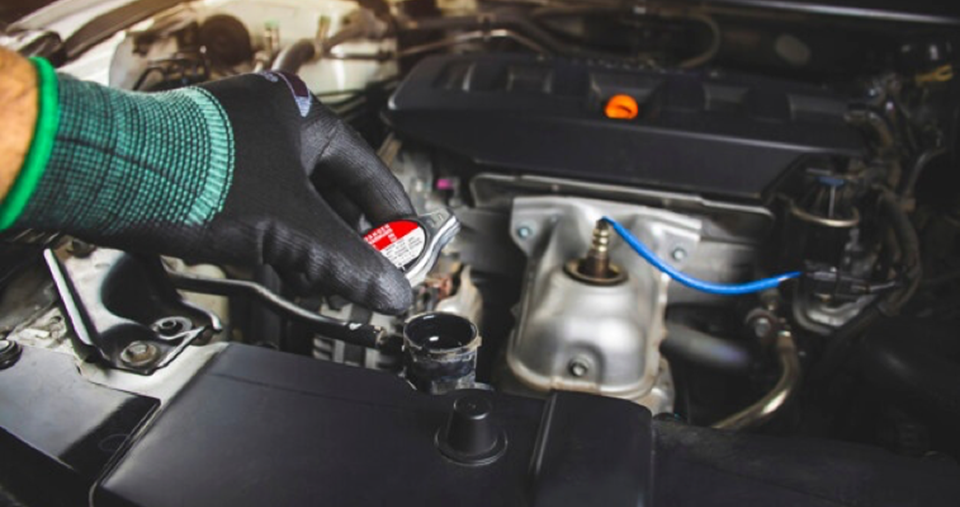
Automotive injection molding provides competitive advantages
The latest tendences see the replacement of heavy metal parts with plastic elements born out from injection molding for a variety of reasons.
Plastic components are:
- Lighter-weight than metal ones
- Cost saving – overall cost usually decreases the more parts are made, thus for mass production applications, automotive injection molding is beneficial to the manufacturer
- Easily repeatable – the robust metal molds we produced guarantee the production of great quantities of identical items, easily meeting the needs of big and medium-sized productions
- Aesthetically pleasant as many surface finishing options and textures can be applied to the molds
Idea Stampi injection molding bonus points for the automotive industry
To the above mentioned advantages of automotive injection molding, we can add a few cherries on top:
- We provide injection molds not only for mass production, but also for tiny, niche production
- We offer a prototyping service and pilot molds so to check functionality on parts before building the definitive mold
- We also produce 100% custom molds so to make you able to deliver product with peculiar shapes and extremely high aesthetic qualities
Last, but not least, if you need us to start your production of plastic elements for the automotive industry, please note that we also offer a service of thermoplastic injection molding service from start to finish, from the pre-production of batches to the delivery of your finished products.
Are you searching for automotive plastic molds or injection molding services? We have what you need!
Contact us for free